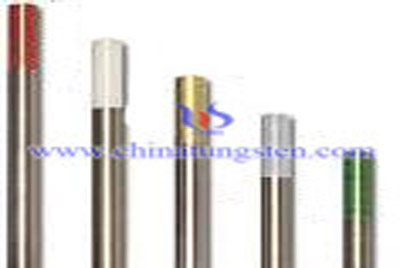

Tip Choices for Tungsten Electrode
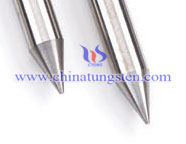
A balled tip is generally used on a Pure tungsten electrode and is suggested for use with the AC process on sine wave and conventional squarewave TIG welders. To properly ball the end of the tungsten, simply apply the AC amperage recommended for a given electrode diameter and the ball on the end of the tungsten will form itself. The diameter of the balled end should not exceed 1.5 times the diameter of the electrode (for example, a 1/8-in. electrode should form a 3/16-in. diameter end), as having a larger sphere at the tip of the electrode can reduce arc stability and/or fall off and contaminate the weld.
A pointed and/or truncated tip (for pure tungsten, ceriated, lanthanated and thoriated types) should be used for inverter AC and DC welding processes. To properly grind the tungsten, use a grinding wheel specially designated for tungsten grinding (to avoid contamination) and one that is made of borazon or diamond (to resist tungsten’s hardness). Note: if you are grinding thoriated tungsten, make sure you control and collect the dust, have an adequate ventilation system at the grinding station and that you follow manufacture’s warnings, instructions and MSDS sheets.
Grind the tungsten straight on the wheel versus at a 90-degree angle to ensure that the grind marks run the length of the electrode. Doing so reduces the presence of ridges on the tungsten that could create arc wandering or melt into the weld puddle, causing contamination.
Generally, you will want to grind the taper on the tungsten to a distance of no more than 2.5 times the electrode diameter (for example, with a 1/8-in. electrode you would grind a surface 1/4 to 5/16-in. long). Grinding the tungsten to a taper eases the transition of arc starting and creates a more focused arc for better welding performance.
When welding with lower currents on thinner materials (those ranging from .005- to .040-in.), it is best to grind the tungsten to a point. A pointed tungsten allows the welding current to transfer in a focused arc and helps prevent thinner metals, such as aluminum, from becoming distorted. As a note, using pointed tungsten for higher current applications is not recommended, as the higher current can blow off the tip of the tungsten and cause weld puddle contamination.
Instead, for higher current applications, it is best to grind your tungsten to a truncated tip. To achieve this shape, first grind the tungsten to a taper as explained above, then grind a .010- to .030-in. flat land on the end of the tungsten. This flat land helps prevent the tungsten from being transferred across the arc and/or from balling.
In any application, the type and shape of tungsten you use helps determine the arc quality and welding performance you will achieve. Each of the six types of tungsten discussed here bring with it distinct advantages and disadvantages. That’s why, regardless of type of material you are TIG welding or whether you are using an AC or DC process, it is always important to choose your tungsten wisely for each application. Doing so can maximize your TIG welding success and is one of the best defenses against contamination and rework.
If you have any other question or inquiry of tungsten electrode, please feel free to contact us through the following methods:
Email: sales@chinatungsten.com sales@xiamentungsten.com
Tel.: +86 592 5129696/86 592 5129595
More Info>>
tungsten products
Specification for Tungsten and Oxide Dispersed Tungsten electrode for Arc Welding and Cutting